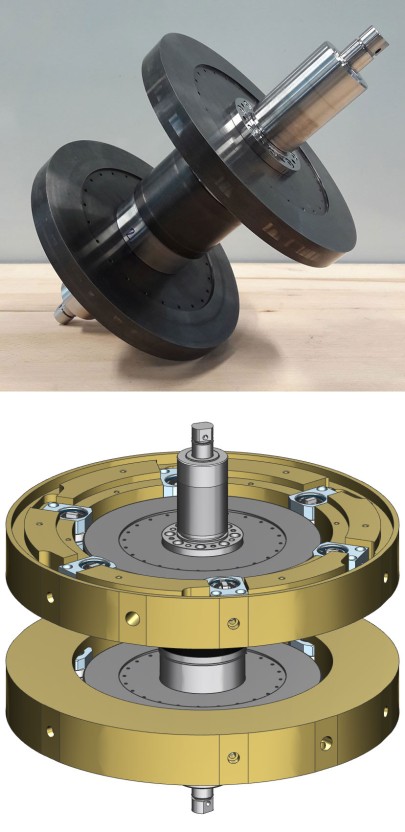
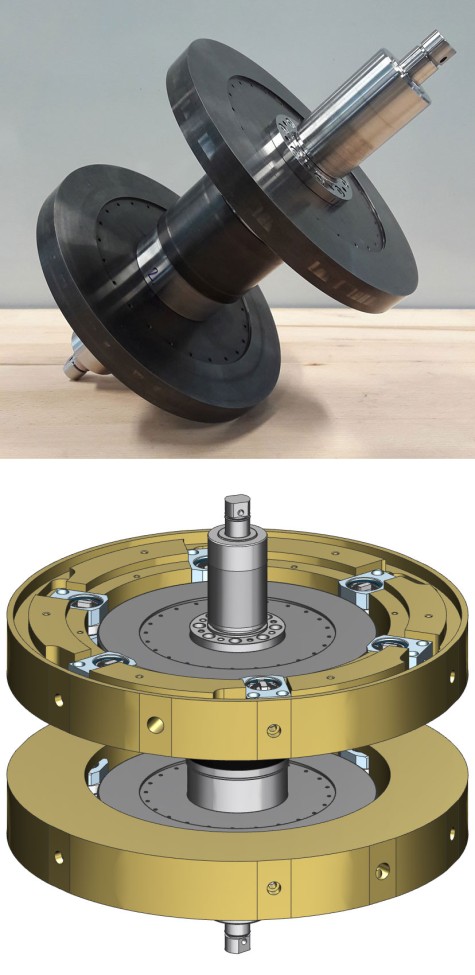
The test rig offers an optimal environment to test the touch-down bearings in different designs, which are highly stressed in case of a rotor drop-down. The test rig is designed as inner rotor, but the rotor dynamic properties are similar to the in external rotor design developed at the IMS. The magnetic bearing consists of two radial and one axial active magnetic bearing, controlled by a magnetic bearing amplifier. The rotor is accelerated and decelerated by a permanent magnetic synchronous machine. By the integrated sensors the speeds and temperatures of the touch-down bearings are recorded. In addition, the contact forces between the rotor and the touch-down bearing unit is measured to obtain information about friction and wear. In this way, the economic efficiency and availability of these mechatronic systems can be increased in the future. The test rig concept is characterized by a robust and modular design with active magnetic bearings. flywheels
By drop-downs into different touch-down bearing configurations, it is possible to determine specific factors influencing the rotor behaviour in connection with the service life of the touch-down bearings. The goal is the validation of the simulation environment in order to design touch-down bearings in different configurations for new systems. ANEAS